The Value of Thorough Welding Examination in Industrial Applications
In the realm of commercial applications, the importance of thorough welding inspection can not be overemphasized. It plays a vital function in guaranteeing the structural honesty and long life of welded components. Advanced non-destructive screening strategies enable the early detection of prospective problems, such as splits and incomplete fusion, which, if left untreated, can result in devastating failings. In addition, adherence to rigorous sector requirements not only assures top quality yet additionally develops customer self-confidence. As we explore the diverse advantages of persistent welding examinations, one have to consider the wider ramifications on safety and security, dependability, and cost-effectiveness in industrial operations.
Enhancing Structural Integrity
When it comes to welding examination in industrial applications, boosting structural integrity is extremely important. The main goal of welding inspection is to make certain that the welds are capable of bearing the anticipated tons and tensions they will come across in solution.
The relevance of keeping structural integrity in welded structures can not be overemphasized. Badly executed welds can bring about tragic failings, causing pricey repair services, downtime, and even endangerment of human lives. For that reason, examiners play a vital duty in the lifecycle of commercial components, providing assurance that the welding process delivers the preferred toughness and durability.
Furthermore, advanced technologies, such as phased array ultrasonic testing and digital radiography, deal improved abilities in finding potential weak points, enabling corrective actions prior to issues escalate. By prioritizing the honesty of welds through careful assessment, sectors can guarantee operational performance and expand the long life of their framework.
Identifying Welding Flaws
Identifying welding flaws is an important element of making certain the security and integrity of bonded structures. These flaws can compromise the integrity of the entire setting up and, if left unaddressed, may cause tragic failures. Typical welding problems include porosity, splits, insufficient blend, and damaging. Each of these flaws arises from particular causes, such as improper welding methods, contamination, or inadequate heat control.
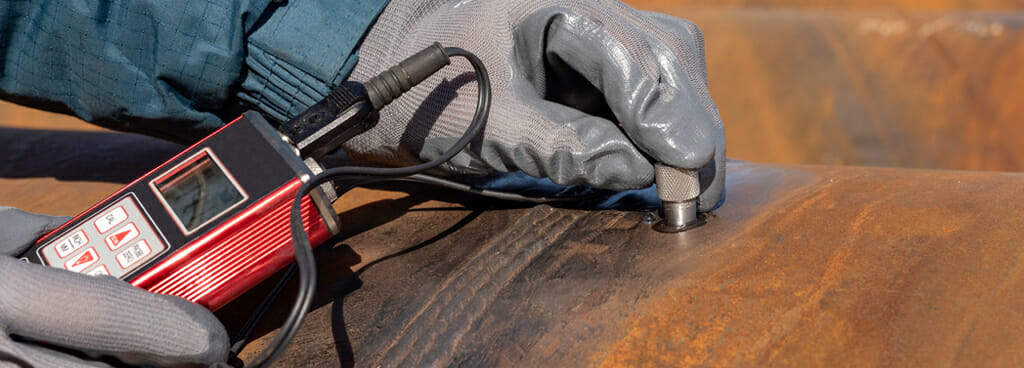
Knowledgeable examiners utilize both visual examination and advanced non-destructive testing (NDT) methods, such as ultrasonic or radiographic testing, to detect these problems. The prompt identification and rectification of welding issues are imperative to maintain the architectural stability and long life of industrial components.
Guaranteeing Compliance Specifications
Maintaining the integrity of bonded frameworks expands past determining issues; it calls for adherence to strict conformity standards. Conformity with established requirements, such as those supplied by the American Welding Culture (AWS) and the International Company for Standardization (ISO), makes sure that welds satisfy minimum find safety and high quality needs. These criteria incorporate a variety of criteria, consisting of material requirements, welding treatments, and credentials of welders. Adherence to these requirements is crucial to stop structural failings, which could cause tragic consequences in industrial applications.
Normal audits and examinations are essential in confirming compliance. Examiners must have a detailed understanding of the relevant criteria and be skilled at making use of different non-destructive screening (NDT) approaches to evaluate weld quality. By making sure that welding methods align with conformity criteria, firms minimize the danger of non-conformity, which can bring about legal liabilities and safety risks.
In addition, maintaining compliance not only safeguards architectural integrity but additionally boosts a company's online reputation in the sector. Customers and stakeholders are most likely to trust fund companies that constantly demonstrate a dedication to quality and security through strenuous conformity. Thus, making certain compliance criteria is a critical part in the successful execution of welding in commercial applications.
Reducing Maintenance Expenses
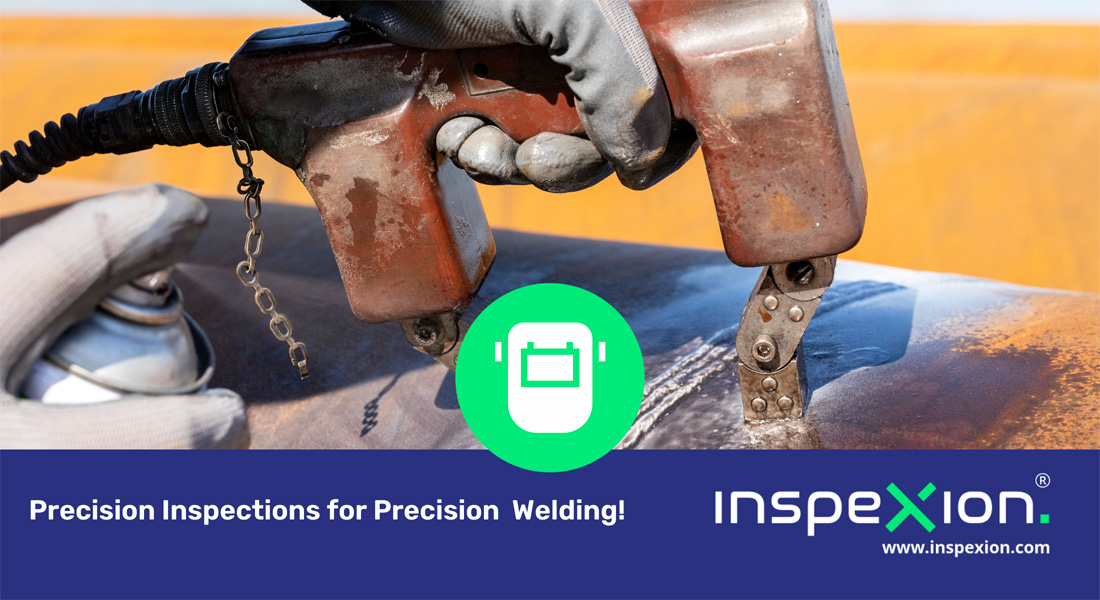
The application of advanced non-destructive testing (NDT) great post to read methods, consisting of ultrasonic, radiographic, and magnetic bit examinations, enhances the ability to discover subsurface imperfections without compromising the structural integrity of components. By using these strategies, sectors can significantly extend the service life of their devices, minimizing downtime and the connected monetary worry of maintenance tasks.
Moreover, a robust welding examination regime supports the optimization of upkeep schedules, changing from reactive to predictive upkeep approaches. This positive method not just stops unforeseen failings yet additionally enhances resource appropriation, guaranteeing that maintenance efforts are focused and effective. Inevitably, the financial investment in rigorous welding evaluation is countered by the substantial cost savings understood through decreased upkeep needs, contributing positively to the overall functional effectiveness of industrial ventures.
Improving Security Steps
Welding examination plays a vital role in this context, as it makes certain that all joints and links satisfy strict safety and security standards. Comprehensive evaluations assist determine flaws such as splits, porosity, or incomplete combination that can compromise architectural stability.
To enhance security procedures, embracing innovative non-destructive testing (NDT) methods is essential. Approaches like ultrasonic testing, radiographic screening, and magnetic bit assessment enable detailed exam without damaging the framework. These innovations allow examiners to identify surprise defects early in the building and construction process, helping with timely corrective activities. Additionally, carrying out a robust top quality control system that consists of regular training for welders and examiners makes sure adherence to established security requirements.
Lastly, promoting a culture of safety within the company emphasizes the importance of comprehensive welding examinations. Motivating open communication and cooperation amongst assessors, designers, and welders adds to a shared dedication to security quality. Welding Inspection Madison. In doing so, markets can secure their operations, shield personnel, and maintain public trust fund

Conclusion
Comprehensive welding evaluation is vital in industrial applications, considerably improving structural honesty and reliability. Ultimately, the diligent execution of welding examinations plays a critical role in maintaining functional performance and safety in industrial settings.
As we explore the complex benefits click over here now of thorough welding assessments, one have to consider the broader ramifications on security, reliability, and cost-effectiveness in industrial procedures.
The main goal of welding examination is to guarantee that the welds are capable of bearing the anticipated anxieties and loads they will experience in solution. Efficient welding inspection plays an integral role in minimizing these expenses by ensuring the integrity and durability of welds, thereby minimizing the risk of early failures.Complete welding assessment is essential in commercial applications, considerably enhancing architectural honesty and dependability. Ultimately, the persistent execution of welding inspections plays an important function in maintaining functional efficiency and safety and security in industrial settings.
Comments on “Why Select Professional Welding Inspection Madison for Your Tasks”